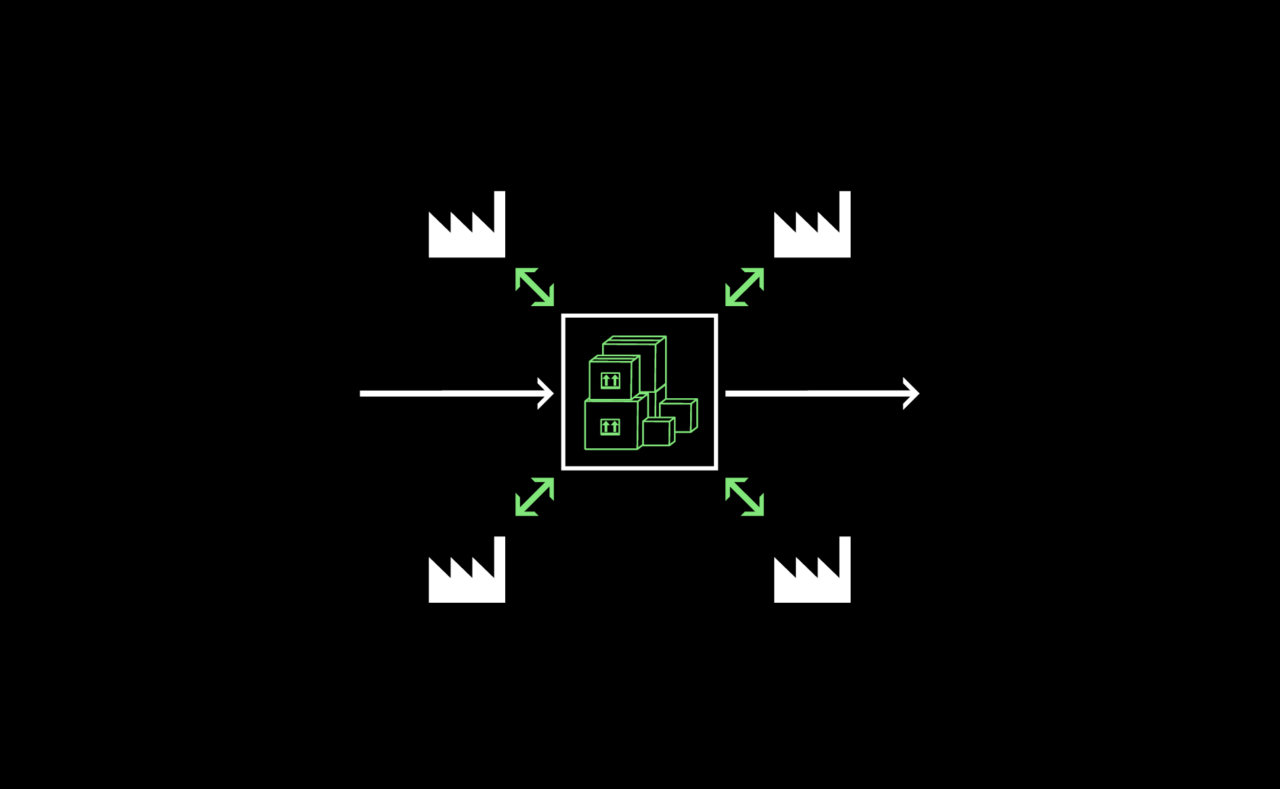
N.6 Centralised Logistics Zone
Central collective logistics space in accessible locations facilitates efficient delivery and discharge of goods while providing opportunities to store material or manufactured goods.
[Context] Traditionally businesses managed logistics in-house, which requires storage facilities, drivers and vehicles. Businesses, especially smaller SMEs, commit ‘unproductive’ working space to storage of materials, manufactured goods (stock) and waste. Reducing on-site storage space could allow for greater amounts of on-site production, greater numbers of employees and a more competitive market share for some businesses. It can also simplify the focus of the company on production of things rather than adding pressures from complex logistics. This is possible only if storage space could be easily shifted off-site while subcontracting logistics. Centralised logistics promotes economies of scale, which can be especially relevant to SMEs. Manufacturing is changing as businesses choose to outsource logistics. This is especially relevant for urban manufacturers where land is at a premium and where in-house logistics provides little benefit for the business. If many businesses adopt this approach, there is value in considering a series of metropolitan scale logistics hubs where goods could be dispatched, which involves storage and is a way of transferring logistics from large vehicles to smaller ones. Such hubs may also be coupled with other activities that can take advantage of logistics like repair or waste management.
[Problem] Firstly, while a centralised logistics zone may seem sensible and feasible, changing logistics habits can be challenging for some businesses. Secondly, the outsourcing of logistics could result in a net increase in traffic due to dependence on just-in-time production and reduction of storage spaces within manufacturing sites. This can defeat part of the benefit of centralising logistics. Finally, the implementation of circular practices in manufacturing, implying the re-use of leftover materials (both on site or by other manufacturers) adds pressure on manufacturers to dedicate extra storage space for reusable goods/materials, service take-back and waste segregation. This makes not having a centralised logistics zone a challenge for R.6 Sustainable Product Cycles.
[Forces] R.8 Moving Things Efficiently often requires more than a single business to be onboard. Value is created when pooling logistics needs from a large number of businesses who would otherwise be wasting time and money with small deliveries and while generating emissions, air pollution and contributing to congestion. Manufacturers are increasingly outsourcing their logistics to improve the efficiency of their distribution system, reduce or streamline costs and specialise on the production process. Improving urban logistics could even be a disadvantage to urban manufacturers as imported products become even cheaper and more accessible. Furthermore, demand for logistics spaces can be in direct competition with manufacturing. While B.8 Space for Storage, is key for all businesses, the level at which this is required can vary a lot between one business and another. Therefore developing a centralised logistics zone may not be useful for businesses immediately and/or may take an extended amount of time for the businesses to adapt to. This will make investing in a centralised logistics zone risky and best done by a public actor that can afford to recuperate costs over the long-term if there is a public benefit of centralising logistics (such as carbon emissions, reduction in congestion or improve efficiency of industrial neighbourhoods).
[Solution] Create a centralised logistics zone to reduce manufacturers’ needs for idle storage while encouraging more efficient movement of goods and resources. A city may have a plan for R.8 Moving Things Efficiently, which is in their own interest to combat the rise of congestion through logistics vehicles and dealing with air pollution issues. Centralising logistics is a practical way of shifting mobility to smaller and cleaner vehicles. This needs to be considered in the context of C.7 Links to Transport Infrastructure, offering opportunities to reduce reliance on road transport to more efficient and environmentally adequate options, including the use of train, trams, canals and waterways. Electric and alternative vehicles (such as bikes) may be considered for inner city deliveries, ensuring low emissions and flexibility avoid getting caught in traffic. Storage often can be combined with other quieter land uses if congestion and noise are well managed (for example with a B.2 Yard for Logistics). If well considered within a master plan to avoid unnecessary conflict (a C.1 Microzoning), logistics can be easily combined with housing or commercial activities. N.5 Local Collection Points of Segregated Waste and R.7 Multi-scalar Circular Infrastructure can be used to bundle logistics with circularity, where logistic centres can also act as reservoirs of used resources and materials. Public authorities interested in centralised logistics zones will likely require strong centralised planning tools and top-down application to avoid double handling goods and creating unnecessary congestion with smaller vehicles.
[Contribution] Add contributions here.