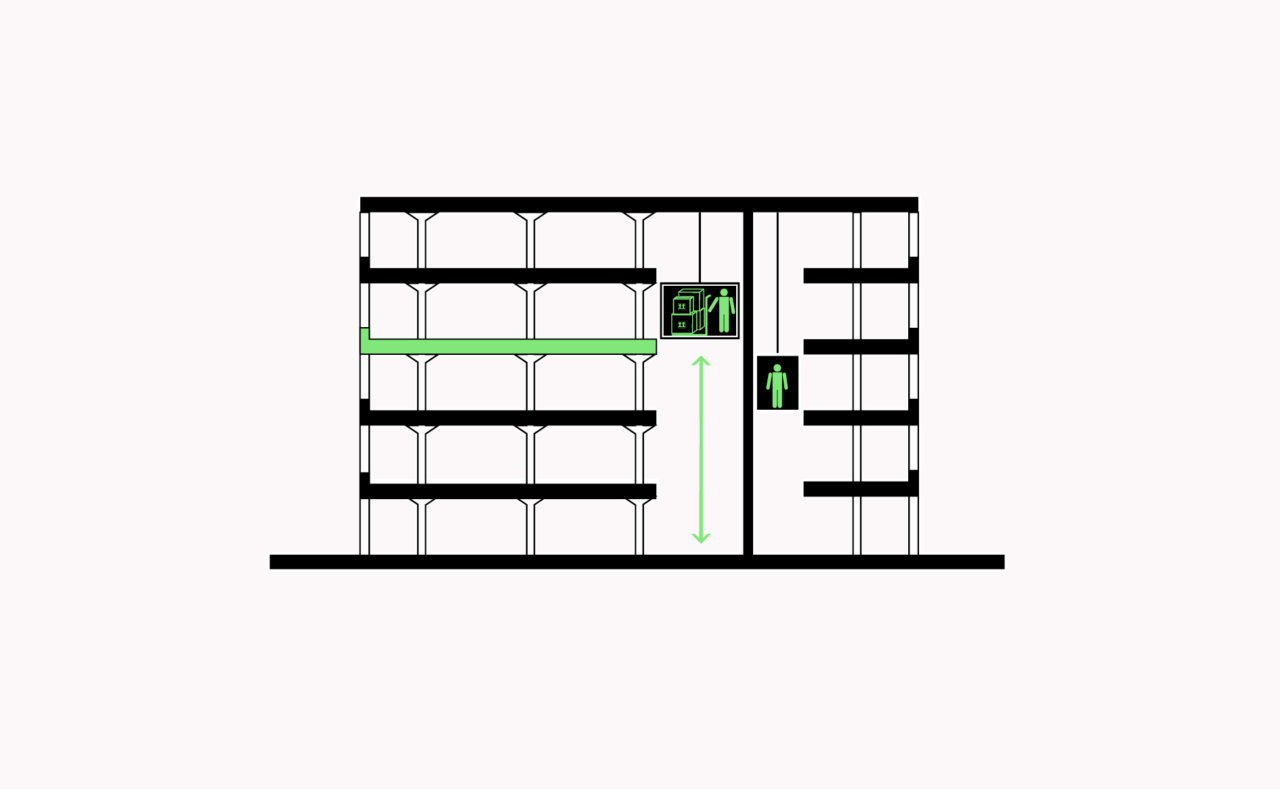
B.5 Enabling Vertical Making
Goods lifts and heavy load-bearing floors in multi-storey buildings allow for industrial intensification and for buildings to adapt according to demand for space.
[Context] During the industrial revolution, the need for direct access to sources of power, water, labour and logistics infrastructure, with limitations of personal transport gave rise to vertical production spaces and compact industrial districts. Subsequent advances in transportation (such as the car) and technical networks allowed businesses to relocate to cheaper and larger industrial sites, functioning generally on one floor. Despite costs and engineering challenges, vertical production sites have a number of advantages over single story sites and are increasingly an attractive option for cities looking to retain or support their manufacturing sector. Vertical manufacturing can allow for a large concentration of expertise and knowledge to be located on a small site, which is useful for nurturing informal relationships between makers and supporting services such as design, distribution or communications. In this sense, vertical making can distribute production spaces relative to weight, need for logistics and noise, thus installing heavy machinery on ground floors while locating offices and meeting spaces on the upper levels.
[Problem] As there is a revival in vertical manufacturing, existing facilities include mixed-activity complexes, or even P.5 The Work Home, are old and unsuited to modern manufacturing Makers struggle with issues such as: R.8 Moving Things Efficiently and B.6 Easy Loading & Unloading, due to the lack of goods lifts, the lack of cranes and B.9 Large Openings, small spacings between columns and unsuitable logistics docks. Retrofitting existing buildings comes with challenges and complications in using certain machinery due to safety concerns (particularly fire or explosions), noise, vibrations or engineering limitations for heavy machinery. Some cities are beginning to compensate the loss of industrial surface areas by proposing ‘industrial intensification’. New buildings can be designed to minimise nuisances and allow for mixed use, even between manufacturing and housing. However stacking industrial activities requires a clear understanding of technical solutions to avoid nuisances and conflict. This is problematic for both public authorities and designers who have little practical experience with such complexity.
[Forces] Industrial intensification or co-location of functions in certain areas (such as C.10 Transition Zones or C.1 Microzoning) comes with certain limitations to manufacturers which should be taken into consideration. Firstly, co-location and intensification limits the availability of large single floor spaces which can be necessary for certain production processes. Public authorities should carefully consider future occupants before approving legislation. Some activities may be problematic due to fire regulation, such as pharmaceutical or chemical related manufacturing. Vertical production requires engineering solutions to manage the extra weight which results in more columns or walls. This can limit flexibility and efficient use of space in terms of the layout of the workspace, limitations of the use of some machines that need continuous surface area and can be challenging for efficient configuration of storage. Management costs can also be problematic. Goods lifts can be expensive or difficult to retrofit in existing buildings due to regulation or structural issues. The overall load-bearing structure needs to be address vibrations, fire safety and logistics.
[Solutions] Where manufacturing occurs on numerous levels, ensure that accessibility (lifts), stability (floor loading), fire protection and interfaces between production and non production spaces do not limit the potential for manufacturing while allowing free and efficient circulation. Technical aspects of vertical making should be carefully considered when developing master plans such as through C.10 Transition Zones, N.3 Mixing Complementary Making & Related Services and C.1 Microzoning to avoid nuisances and tension between land uses. This includes locations for logistics (B.6 Easy Loading & Unloading) and concentration of similar kinds of making (N.9 Making Touches Making). For new buildings to host vertical manufacturing, goods lifts are essential. Provide preferably two or more to account for redundancy, large enough to take a pallet and pallet trolley or forklift, separating flows of people and materials. Provide B.9 Large Openings in combination with lift systems facing the N.11 Back of the High Street or B.2 Yards for Logistics for large and cumbersome objects. Provide suitable B.7 Access to Technical Networks & Services such as ventilation, water pressure and voltage. Include strong load-bearing structures, and flexible floor plans for B.4 Facilitating Horizontal Organisation of production. Provide suitable fire escapes and a range of exits. In the case of mixed use buildings, separating structural systems for different functions can avoid transmission of vibrations. C.1 Microzoning and R.10 Place-based Financial Levers can help solve financial and legislative constraints linked with mixing manufacturing with other uses, installing a goods lift, refurbishing buildings while complying with C.2 Negotiated Qualities & Environmental Criteria.
[Contribution] Add contributions here.