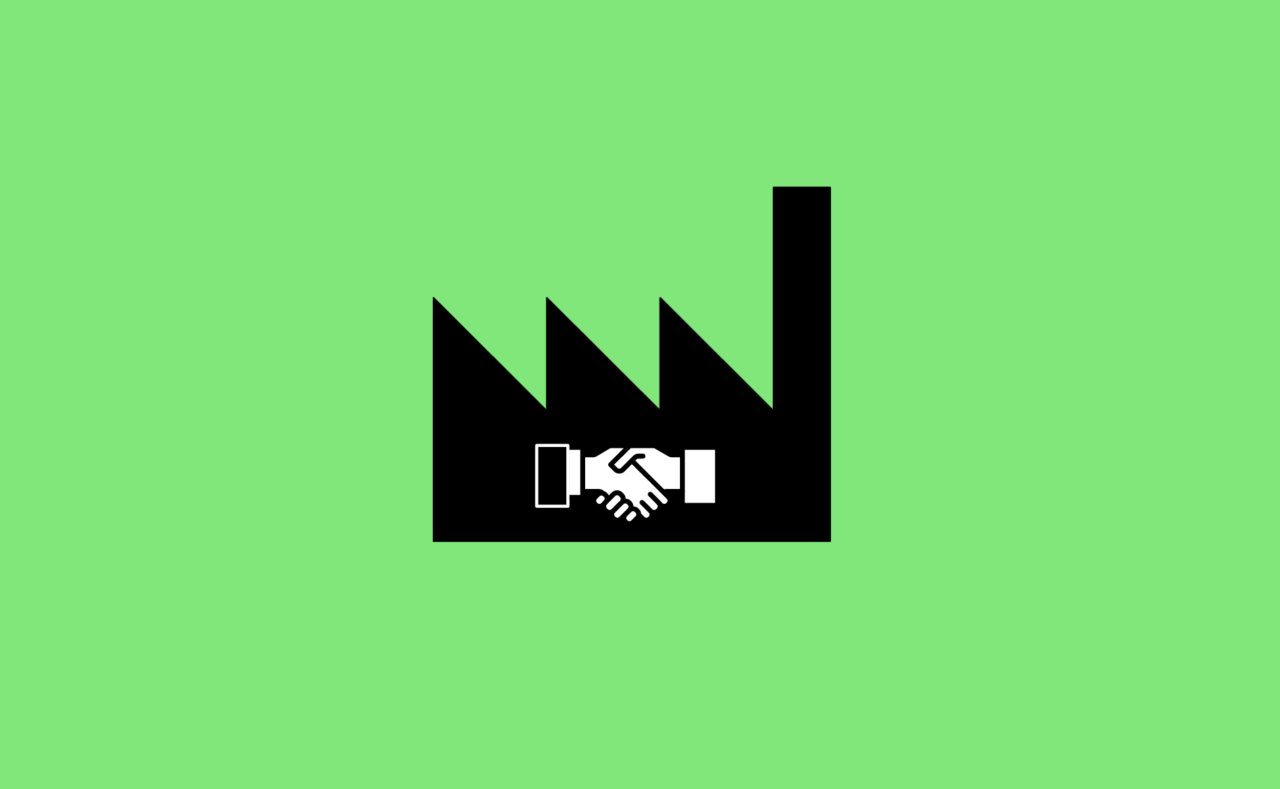
R.5 Fair Work Conditions
Fair working conditions are integral for providing good quality output, a reliable and agile workforce, a strong brand and in turn to promote manufacturing businesses as a valuable source of employment.
[Context] Workers are a critical part of the production cycle and businesses often claim to have a shortage of high-quality workers. Yet workers are in constant tension between the expectations of management in delivering suitable levels of output, adapting to new technology and being subject to the threat of replacement through automation. Jobs are increasingly changing and need to be more reactive to market demands. Conversely, the working conditions can play a significant role in the performance of a worker, which can be linked to the comfort of the job (amount of breaks and the workstations), the length of the working day, the workplace atmosphere, exposure to pollution (noise, dust or fumes), the capacity for independent decision making, the pay level, access to holidays and pension and so forth. Poor work conditions can impact productivity, result in illness or lead to strikes that can paralyse businesses.
[Problems] While manufacturing has changed significantly in many western cities, conditions remain challenging, often involving workers in precarious conditions who’s well-being can affect the quality of the products and the standard of production. Positions are increasingly flexible and paid by the hour (zero-hour contracts), affecting workers capacity to make long-term personal investments. Even if flexibility can be seen to have competitive advantages, uncertainty can degrade relationships between workers and their managers. Low wages have a direct impact on health conditions. In addition, manufacturing remains physically challenging which can involve carrying heavy loads, repetitive strains and extensive periods without breaks. While some low-skilled, low paid and physically challenging jobs will most likely remain in cities, such work may be considered incompatible with the local costs of living and result in moving such businesses to cheaper locations. The knock-on effect will result in a smaller pool of available workers for remaining companies. Conversely, when businesses close or manufacturing processes change, there may be challenges to find related jobs or retrain workers to adapt to similar meaningful work. Retrenched skilled workers can be left both demoralised or isolated and result in radical social consequences.
[Forces] Cities are a great source of labour, but higher urban wages can increase the overall production costs and impact the capacity of manufacturers to compete against imported goods. Manufacturers also compete against services businesses for space, which can produce greater profits on a smaller footprint. Due to high costs, urban manufacturers are often pressed to generate a marginal turnover, which means balancing production costs and providing suitable work conditions, even if their products are ‘foundational’ for the city (such as N.2 Re-use of Material & Energy Flows or P.6 Re-use and Repair Centres). Likewise, businesses may struggle to find suitable skilled labour and be incentivised to replace human labour with labour saving technology. Furthermore, unnecessary labour costs may have arisen from friction with management, poor work conditions, poor work culture or poor training – issues which can be addressed through non-mechanical solutions. Manufacturers may be attracted to labour saving ‘innovation’, where workers are treated as machines and their actions are measured carefully to achieve optimum performance.
[Solutions] Ensure work conditions are dignified, comfortable, democratic and fair to support a motivated workforce. Firstly, job conditions should encourage diversity in the broadest sense, from skill level (R.4 Availability of Diverse Jobs), to ethnicity or sex. Where imbalances occur, manufacturers should do their best (and be encouraged) to invest in diversity. Secondly, business structures could be adapted for profit sharing. Cooperatives can provide incentives for workers to feel responsible to adapt their working conditions to their needs while non-profit company structures can help push down overheads or encourage reinvestment of profits back into the business. Thirdly, the active participation of workers in a business’ decision making process can help to motivate workers while helping them to take responsibility for changes and help them to prepare for change. R.2 Transparent Making can provide legitimacy and avoid miscommunication. Employers can improve quality through introduction of ‘co-bots’ or technical support, helping with repetitive tasks while supporting workers focus on quality control and creative thinking tasks. This also may require adapting the business model, distribution volumes or product pricing to benefit work conditions and improve the quality of products. Inspiring work conditions may offer R.11 Incentives for Research and Development and can be implemented, particularly within larger businesses, to motivate workers to also look for solutions to improve output. P.7 Spaces for Development & Education, in addition to making time available for training, can help workers to build skills on the job and to adapt to new technology incrementally. Commuting times are also an important factor, which can be addressed through C.6 Strategic Access to Multimodal Mobility.
[Contribution] Add contributions here.