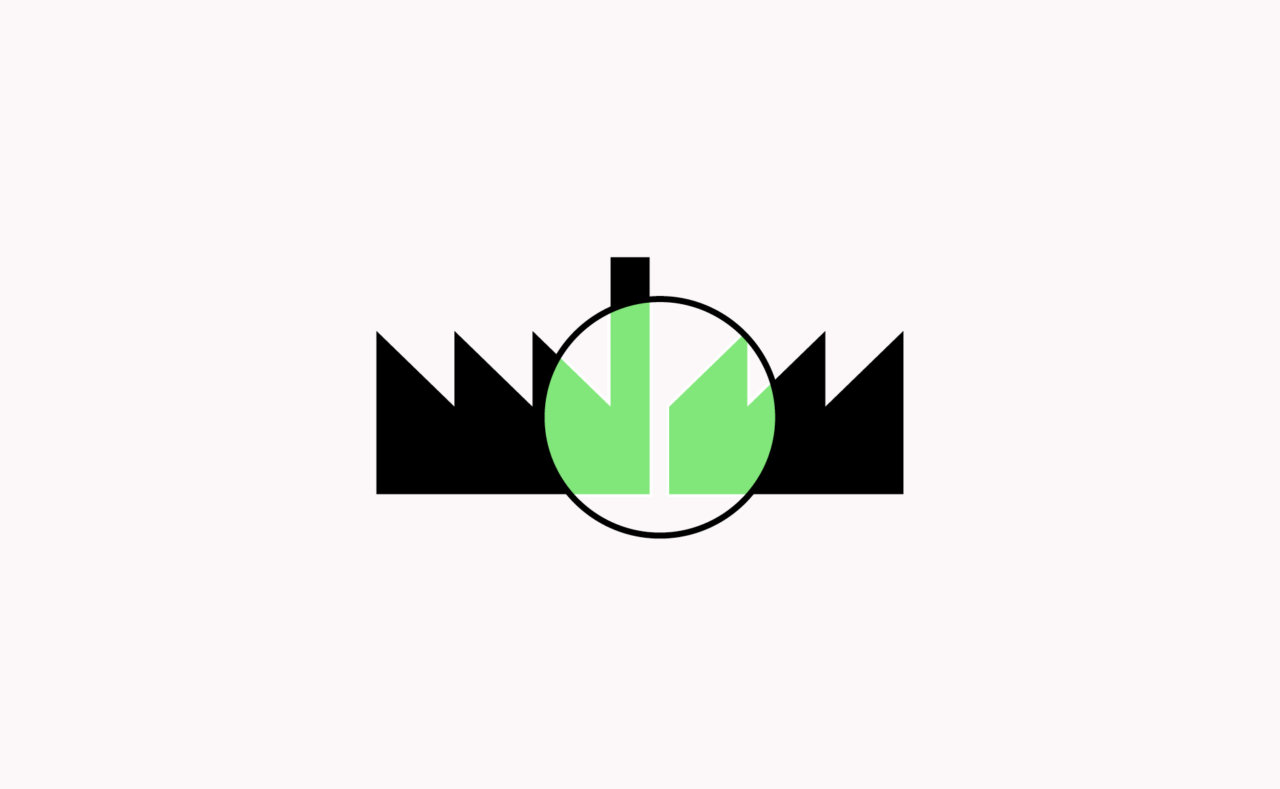
N.9 Making Touches Making
Locating businesses according to similar environmental issues helps to minimise negative impacts of manufacturing by focusing on the block (noise and dust), streets (logistics) or neighbourhood (odours).
[Context] Many forms of urban manufacturing traditionally concentrated along specific streets or clustered in similar parts of the city. It is a trend that is still prevalent due to zoning and land use planning. Protecting these streets as zones of production, particularly in inner-city sites, can help avoid friction or nuisances from incompatible land uses. By contrast, the continuous growth of many European cities and especially the roll-out of designed mixed use areas requires cities to act strategically when planning for the co-existence of different and sometimes incompatible land uses. By concentrating similar kinds of activities along specific streets, nuisances can be contained. This is particularly the case for businesses associated with similar environmental issues such as noise, dust and logistics.
[Problem] Challenges differ between well established streets that are home to manufacturers, and new mixed use projects that are creating industrial space. In cities where manufacturing has remained concentrated around a specific street, these areas are likely to contain large building blocks which are attractive opportunities for rezoning and development into housing. The moment that one manufacturing site is occupied by housing, means that all other sites next to it will be exposed to occupants with very different perceptions of environmental issues and infrastructure requirements. This can aggravate future relationships. Residents are affected by logistics, dust, noise and messy public space resulting from manufacturing. Manufacturers are affected by complaints requiring adaptations to their work spaces with acoustic insulation, invest in low emissions technology, enhanced filtration devices and limiting logistics issues. On the other hand, new mixed use projects can be poorly designed from the outset making it difficult for manufacturing and housing to co-habit. If mixed use developments are a prerequisite, suitable technical and design solutions are required to allow these two activities to live apart, together. Furthermore, developers responsible for mixed use and co-location projects often have little experience mixing residential and manufacturing activities which can mean that financial models and spatial configurations render manufacturing unviable. This results in poorly conceived projects.
[Forces] Increasing pressure on urban real estate and increasing interest in local manufacturing creates an urgency to protect existing manufacturing zones or develop functional mixed use projects with solutions to reduce nuisances and use space more efficiently. For existing manufacturing areas, planning can be challenging to enforce where building owners or developers have (financial and political) means to push through rezoning and housing projects. While plans for mixed use developments can be sensible on paper, it can result in a vast amount of technical complexity that creates unnecessary friction between manufacturers and residents. Unless public authorities have experience in dealing with such projects, there is a high risk that the spaces created for manufacturing will be difficult to use and consequently turn into retail or office space through rezoning. Aligning similar functions along a street can help divide incompatible activities but this requires planners and developers to commit to separating functions. This is a particular challenge in situations where industrial land quotas need to compensate space rezoned for housing.
[Solutions] Concentrate similar types of makers along a street or blocks in order to minimise impact on neighbours. For new development areas, C1 Microzoning can be used to structure activities in specific zones using a master plan or vision document. For existing areas, R.2 Transparent Making and C.2 Negotiated Qualities & Environmental Criteria, mediated with a R.3 Curator, can help reduce friction between manufacturers and residents. Manufacturing activities creating nuisances can be located in areas where such nuisances are tolerated. Making touches making is most effectively channelled along a street, but also in the back of industrial plots, at the scale of the block. N.3 Mixing Complementary Making & Related Services is one option to create a buffer between making and housing particularly for noise attenuation within C.10 Transition Zones. Making touches making works well by C.9 Concentrating Messy Making Along Infrastructure, and N.1 Taking Advantage of Place Conditions, developing along transport infrastructure, using topographic height differences to buffer noise or mixed with other compatible land uses. Cluster B.1 Making Around Courtyards inside blocks, by B.5 Enabling Vertical Making and organising logistics access via an entrance on a service street, (such as the N.11 Back of the High Street). If planned properly, making touches making can result in N.8 Quality Urban Environment in Making Areas that do not result in conflict with manufacturing activities. It is important to keep some mix to ensure that streets remain active after typical working hours which could include sporting facilities or a cafe.
[Contribution] Add contributions here.